Strategic Planning Software
As the trading pattern of a
company is constantly changing there comes a need from time to time to re-deploy the resources required to service customers.
Historically this may lead to overlap of depot areas and in some cases the need to close or re-locate depots.
In many cases stock-holding depots can be replaced by simple transhipment points.
This Module looks at the distribution operation over a period of time - several days, weeks, or even months. The programming
techniques used ensure that unnecessary computation is eliminated and that execution times are short - so allowing many alternative
strategies to be examined quickly.
The DiPS Software conducts optimisation analysis to reallocate demand (and supply) points to their cheapest depot or supply chain option.
Account may be taken of multiple supply chains with their constituent individual links, product throughputs, costs and resource limitations at each depot.
Complimentary modules also enable location of ideal "greenfield" sites and a graphical manual allocation of depot areas.
In DiPS, Vehicle costs are an essential part of both the supply chain analysis and all the vehicle scheduling programs
In the supply chain process, they play an important role in deciding the allocation of calls to depots as the cost for each call from each depot are compared before selecting a depot,
whilst in producing route schedules the total cost values are used to choose the best vehicle, with the cheapest option chosen from a list of acceptable alternative types.
For more information on Costing click this link
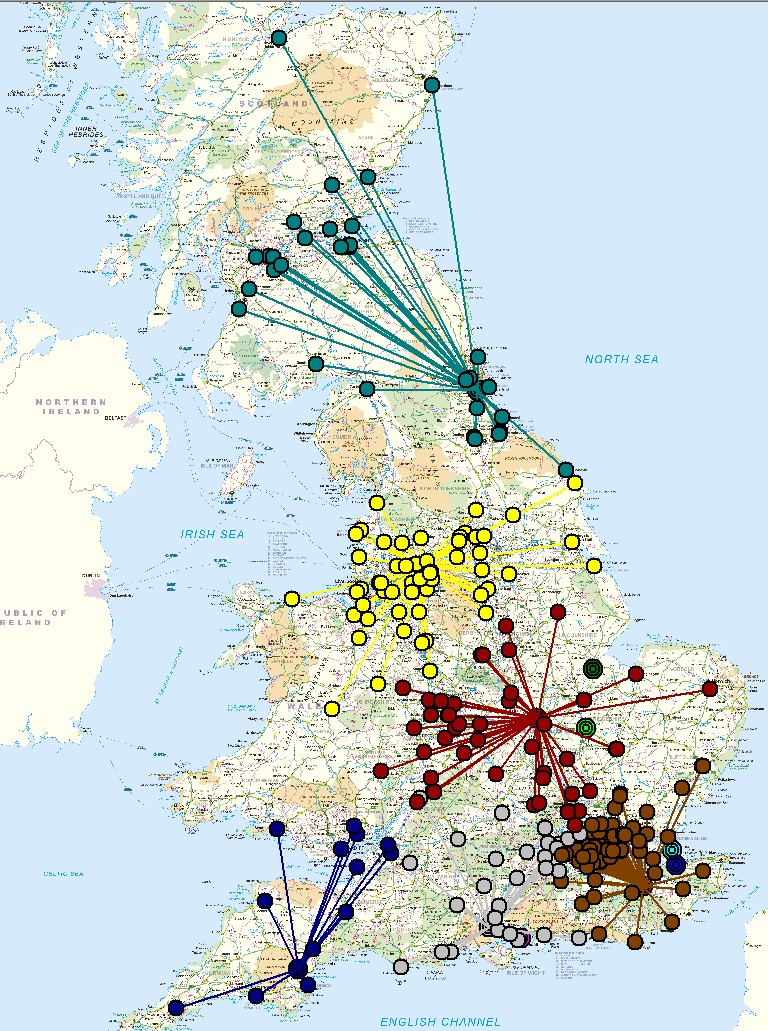
Supply Chain & Depot Location
This module will choose the best method of utilising a given depot supply-chain network to minimise the operating costs defined,
looking at a period of time ranging from several days to weeks or even months. The allocation of accounts is fully integrated with
the DiPS Strategic Route Planning System to allow immediate scheduling.
Complete depot structures may be modelled to reflect different product "paths" from origin to destination.
Any combination of factory, depot, transhipment point, satellite depot etc. can be represented.
It is possible to define a comprehensive set of cost parameters to cover all aspects of an operation.
Account is also taken of the maximum resources available on each link of the supply-chain and at each depot.
Many levels of product supply and demand are catered for with the ability to merge and factor volumes by product type.
Even carriage paid supply and delivery can be included to measure the trade-off between own fleet and third party operations.
The actual algorithm can be modified by the user and typically takes any or all the following into account :-
* Costs - Local, Trunk, Handling and Third Party
* Actual road system in the area
* Fleet size at each proposed depot
* Proximity of calls to depots and marginal costing
* Work standards
* Vehicle size constraints
* Opening times in conjunction with stem times
* Economics of using transhipment points or sub-depots to meet the following criteria :-
* Minimum cost
* Maximum fleet utilisation
* Minimum travelling for each load
* Obeying all restrictions placed upon the system
* Sensible shaped boundaries
* Service levels required.
Vehicle Scheduling
This module provides the means to model the entire distribution operation of a company at the finest level of detail, minimising
travelling time and maximising vehicle utilisation. It may include one or more depots in each run thus enabling a combined trunking and
multi-drop operation to be investigated.
Full account is taken of all constraints placed upon the problem ranging from vehicle capacities, depot and call opening times,
travel and work standards, to legal restrictions on shift and break times. Since no two distribution problems are the same, a number of
control parameters have been provided to enable users to achieve results appropriate to their particular problems. These controls not
only define the algorithm to be used but also reflect the decision criteria generally practised within a company's traffic office.
In exploring the effects of changing aspects of the distribution system the following investigations are commonly undertaken :-
* Mixing different types of trade on the same fleet
* Interaction of several depot areas
* Changes to fleet composition
* Examine the costs of different service levels over a number of weeks
* Plans for peak/trough operations
* Profitability analysis of each account
The results produced contain detailed
information such as travel and work times, arrival times and departure times and resource summaries over a period of weeks if
required. All reports may be exported to spreadsheet and database programs.
Once the scheduling run is complete these routes will be saved on the central database, where the load planner may amend the routes
using "Drag and Drop" facilities to easily transfer Calls, Vehicles and Trips between any number of routes. All the required checks are
made on time and load constraints using the road network travel times and warning messages advise the user of anything illegal.
Visual displays for Calls not assigned to Trips by varying priority ensure that nothing is missed from the plan. Re-optimisation of the
calls in a route is provided as an option.
Over 21 years of working closely with customers has led to enhancements including: optimising remote garaging and reload
points; scheduling draw-bar demountable body operations which allow access to restricted delivery points with or without the trailer
section; and planning multiple depots and vehicle fleets where vehicles from one depot may be further utilised by other depots to
collect and deliver product before returning to their initial starting location.
For further information about DiPS software packages please contact us using the details below:
Support: support@dips.co.uk
Sales: sales@dips.co.uk
Tel: 0333 577 0367